Plus haut, plus vite, plus loin ! Les exigences des clients de l'entreprise technologique finlandaise ETRA Oy (ETRA), qui propose à ses clients une large gamme de produits et de services industriels en tant que grossiste et détaillant, ne cessent d'augmenter et requièrent un niveau de qualité et de fiabilité optimal à tout moment. C'est pourquoi ETRA a délibérément opté pour l'automatisation lors de l'extension de la logistique de son entrepôt central de Hämeenlinna (Finlande).
Avec l'extension de son centre logistique et l'implémentation du WMS (Warehouse Management Software) SuPCIS-L8, ETRA a déjà franchi des étapes décisives vers l'ère numérique. Les processus que le WMS SuPCIS-L8 reproduit et prend en charge comprennent tous les processus et composants dans les zones de stockage automatisées, de la réception des marchandises à l'emballage en passant par la préparation des commandes avec système pick-to-light intégré et la consolidation. Grâce à l'interaction parfaite du WMS et du MFC avec les commandes d'installation de Gebhardt Fördertechnik GmbH, ETRA bénéficie d'un flux de matériel sur mesure et efficace.
Le nouveau système AKL (entrepôt automatique pour petites pièces) à double profondeur et à 4 allées offre une vaste surface utile et environ 50.000 emplacements de stockage pour la large gamme de produits stockés. Les marchandises arrivant de la réception centrale ou le réapprovisionnement des zones de stockage manuel sont reconditionnés, selon la quantité et la configuration dans la base de données articles du WMS, dans les conteneurs automatisés et mis à disposition par le WMS, dans la quantité proposée par le WMS. Deux types de conteneurs différents sont disponibles à cet effet. Si nécessaire, ceux-ci peuvent également être subdivisés pour le stockage de plusieurs articles par conteneur. Cette subdivision est également visualisée graphiquement dans les processus. Mais avant de pouvoir être stockées, les marchandises sont soumises à un contrôle de poids et de hauteur. Le poids maximal de 50 kg est également contrôlé et aucun matériau ou emballage ne dépasse des bacs.
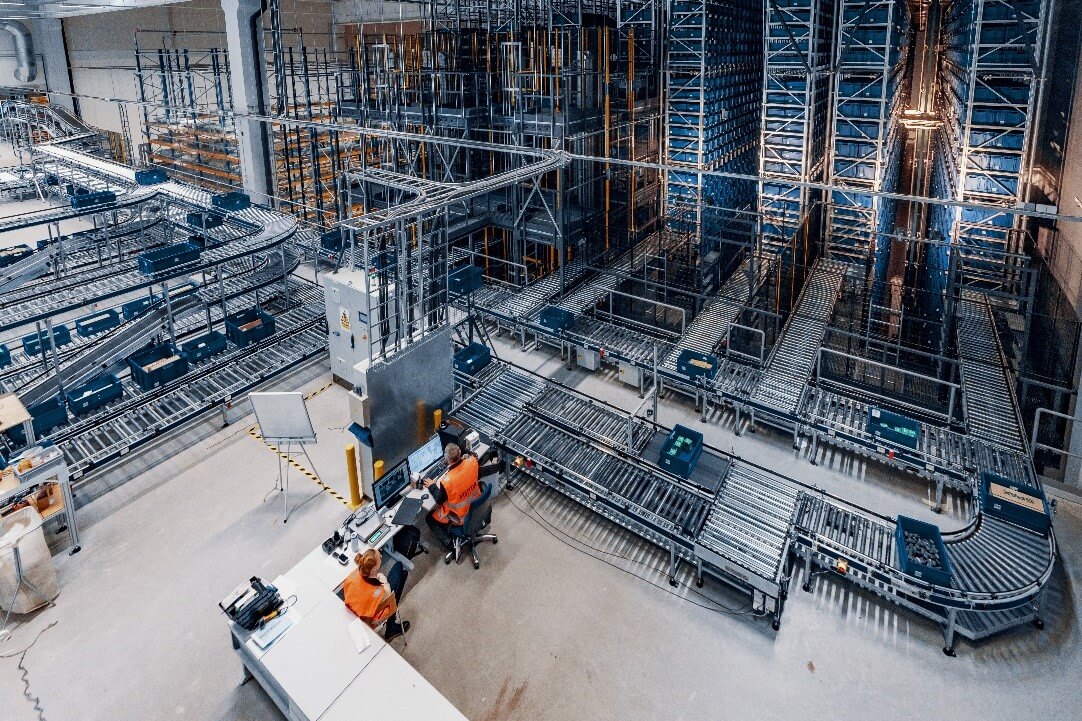
En cas d'erreur, les conteneurs sont directement remis à l'opérateur avec indication de l'erreur. Pour les petites quantités, il est également possible de demander à l'un des postes de reconditionnement des bacs de stockage peu remplis pour les stocker.
Sur les quatre allées de l'AKL, deux sont exploitées par des RGB (transstockeurs) de Gebhardt Fördertechnik et servent de zone pour les marchandises qui ne tournent pas à grande vitesse et qui sont stockées en grande quantité. Les deux autres allées sont utilisées pour stocker des conteneurs d'articles à forte rotation. Cinq MLS (Multi-Level-Shuttle) superposés y opèrent respectivement et sont approvisionnés et évacués par un ascenseur. Cette mise en parallèle permet d'augmenter considérablement la capacité de stockage. Chaque chariot, ainsi que les trois systèmes de commande des zones de manutention, sont directement couplés au SuPCIS-L8 MFC.
Afin d'améliorer également les performances lors du stockage, le transstockeur et le MLS disposent de la possibilité de transporter deux conteneurs simultanément. La sélection des emplacements de stockage est optimisée par le WMS de manière à prendre en compte aussi bien l'occupation actuelle des tampons avant les niveaux que l'occupation des emplacements à l'intérieur des allées ainsi que la formation de paires pour le stockage en double profondeur.
Processus logistiques rapides et transparents
Le WMS gère aussi bien le nouvel AKL que la zone de préparation des commandes et de stockage déjà installée auparavant avec 32 tours de stockage Kardex et la technique de convoyage Gebhardt en amont. Le WMS s'est ici intégré dans l'interface existant à l'origine entre la commande Kardex et l'hôte, tout comme dans celle entre Kardex et la commande de manutention existante. La nouvelle fonctionnalité a ainsi pu être obtenue sans intervention sur les systèmes existants. Si une commande nécessite des marchandises des deux secteurs, la marchandise est d'abord préparée dans le secteur Kardex et stockée temporairement dans le tampon de consolidation, également automatisé au moyen d'un Shuttle multiniveau. Ce n'est qu'à ce moment-là que le WMS commence à prélever les pièces de la commande dans le magasin automatisé.
Les conteneurs source individuels sont ensuite acheminés par le système de convoyage vers les six postes de travail de préparation de commandes "Marchandise à la personne", qui comportent chacun quatre postes de destination pour les conteneurs extra-larges, utilisés uniquement pour le transport entre le poste de préparation de commandes et le poste d'emballage. Ces conteneurs sont mis à disposition de manière automatisée et mariés à l'emplacement de destination. Le WMS planifie ici les commandes volumineuses sur des conteneurs individuels et les commandes à une position pour réduire le transport sur le convoyeur entre le prélèvement et la zone d'emballage sur des conteneurs collectifs. L'image du produit est affichée à l'employé qui prélève la marchandise dans la quantité indiquée par le système de gestion des stocks. Grâce au système Pick-to-Light installé, le processus de distribution qui s'ensuit est encore plus simple pour les employés, car l'écran installé au-dessus du conteneur indique à l'employé où placer telle ou telle quantité. Il suffit ensuite de confirmer la distribution à l'aide du bouton d'acquittement.
Pour les petits articles qui devraient être comptés en grandes quantités, des balances de comptage entièrement intégrées dans le dialogue SuPCIS-L8 sont utilisées. Le dialogue indique à chaque fois de manière ergonomique combien d'articles ont été pesés et dans quelle mesure il faut encore ajouter ou retirer des pièces. Le dialogue intégré élimine le comptage fastidieux. Dans le WMS, il n'est pas nécessaire de manipuler la balance en plus.
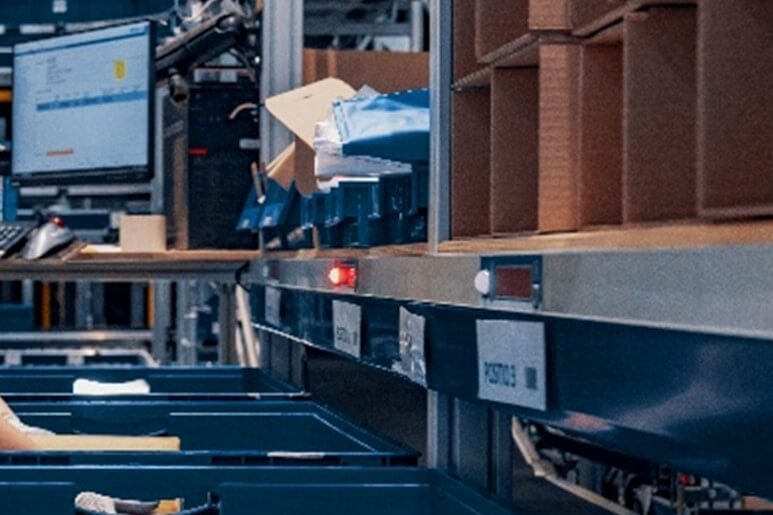
Lorsqu'une tâche est terminée, l'employé en est informé en texte clair via le système PTL. L'employé déclenche l'enlèvement du conteneur cible via l'écran, tout comme l'enlèvement du conteneur source lorsque celui-ci n'est plus nécessaire. Le temps que l'employé revienne au poste de prélèvement, le conteneur de prélèvement suivant est déjà prêt. Selon les besoins, le conteneur source est soit déplacé vers un autre emplacement de prélèvement, soit remis en stock dans le magasin automatique après un passage par zéro.
Les bacs de commande contenant une commande complète, comme les bacs de collecte pour les commandes à une seule position, arrivent directement après le processus de prélèvement via une boucle à l'un des six postes d'emballage. En revanche, si une commande se compose de plusieurs bacs provenant des deux zones de stockage automatisées, une mise en tampon intermédiaire a lieu jusqu'à ce que le dernier bac arrive dans le tampon de consolidation. Le WMS déclenche alors le prélèvement de tous les conteneurs d'une commande vers l'un des cinq postes d'emballage directement accessibles depuis le tampon de consolidation, selon la priorité définie par l'opérateur.
Ceci est très important car les livraisons directes sur les chantiers des clients ainsi que les commandes de réapprovisionnement vers les entrepôts décentralisés et les points de vente ETRA dans toute la Finlande sont effectuées avec des heures de départ différentes de l'entrepôt central. La haute qualité de service d'ETRA exige que toutes les commandes soient livrées prêtes le jour même. Les livraisons de colis sont emballées au poste d'emballage et préparées pour l'expédition. Les livraisons aux points de vente ETRA sont effectuées dans le respect de l'environnement par un système en circuit fermé avec des conteneurs réutilisables que l'emballeur transfère à nouveau sur le convoyeur et qui sont évacués de manière entièrement automatique par des voies de mise à disposition.
Aperçu completde l'état de l'entrepôt
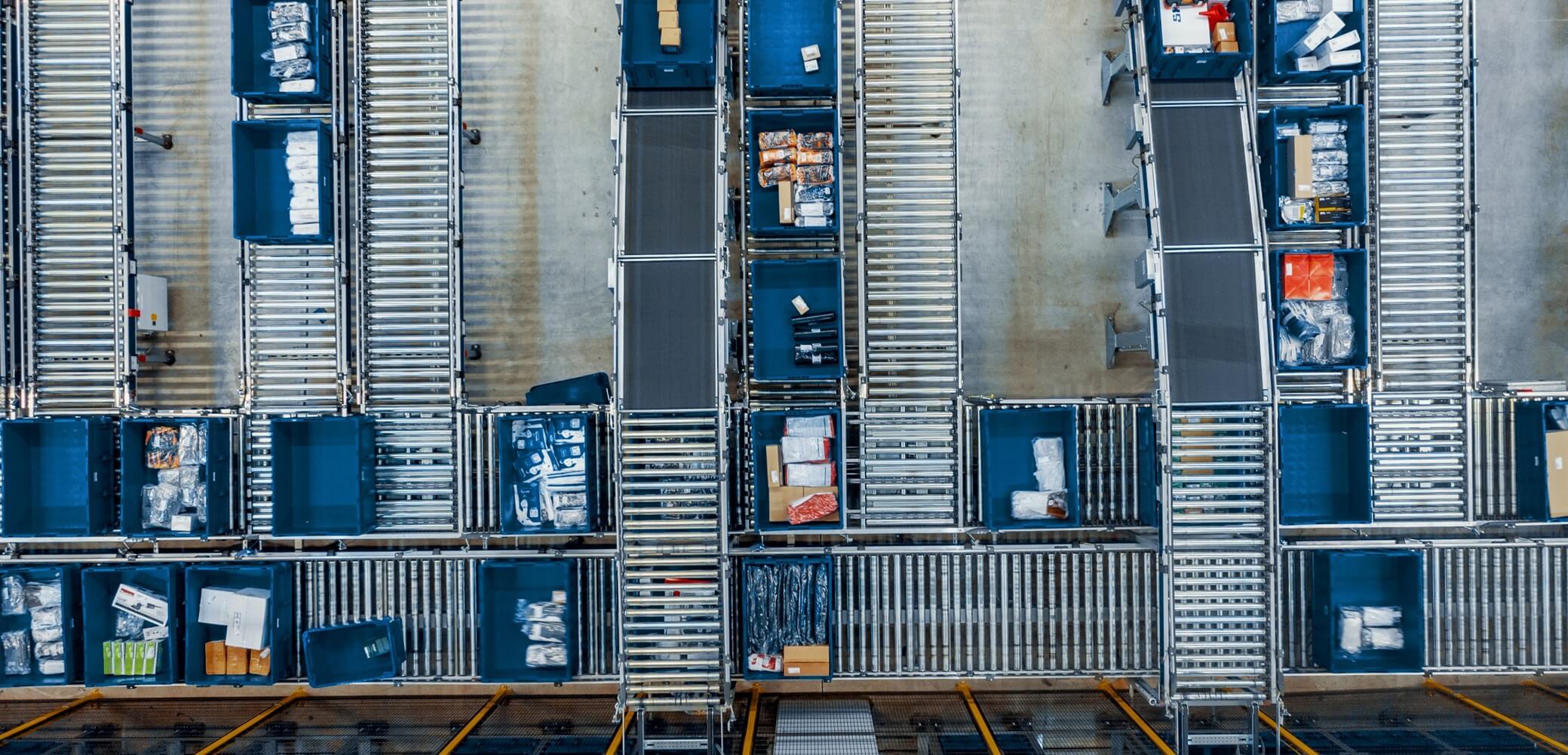
Afin d'augmenter au mieux l'efficacité, la productivité et la transparence dans l'entrepôt d'ETRA et d'éviter les erreurs, le studio photo de SuPCIS-L8 et le Warehouse Viewer sont également utilisés. Le studio photo de SuPCIS-L8 permet de prendre en photo les articles ou les unités d'emballage qui n'avaient pas d'image dans la boutique en ligne. Grâce au traitement d'image intégré, il est également possible de marquer des caractéristiques spéciales, de les afficher dans le système de gestion d'entrepôt et de les enregistrer de manière permanente.
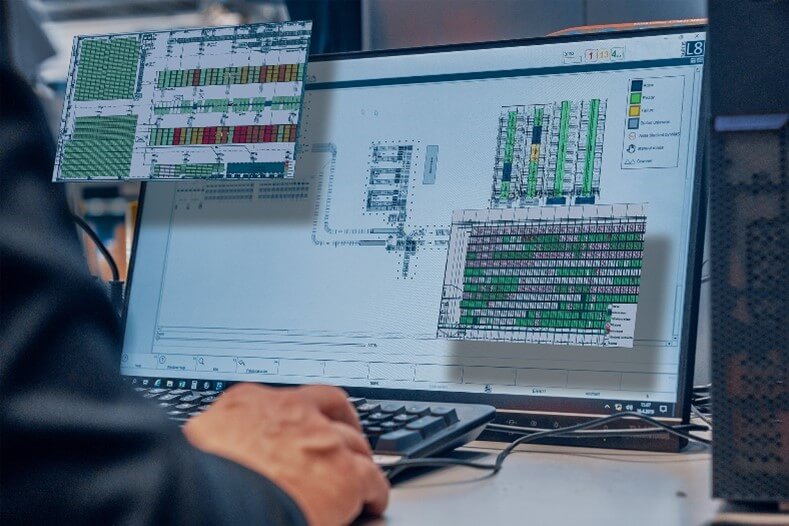
En complément, la visionneuse d'entrepôt offre à tout moment un aperçu graphique des zones de stockage ainsi qu'une visualisation des mouvements et des états des composants d'automatisation utilisés dans l'entrepôt. La consultation d'éventuelles pannes dans l'entrepôt ou de statistiques sur les scanners est ainsi également possible rapidement et facilement à chaque poste de travail du WMS. Le cockpit SuPCIS-L8, avec sa collection de tableaux de bord, affiche les données actuelles sur le nombre de commandes en attente et clôturées, les informations sur le niveau de remplissage actuel des allées, les entrées et sorties de stock ainsi que le statut de la préparation de commandes.
Une stratégie logistique efficace, pivot de l'avenir
L'interaction sans faille entre le WMS SuPCIS-L8 et la technique de convoyage de Gebhardt constitue une solution globale réussie pour l'entreprise. Grâce à la flexibilité, à la personnalisation et aux interfaces disponibles du logiciel de gestion d'entrepôt, ETRA a la possibilité de continuer à développer sa logistique d'entrepôt à l'avenir. "Grâce à l'extension de notre logistique d'entrepôt et à l'implémentation réussie de SuPCIS-L8, nous pourrons continuer à répondre au mieux aux besoins de nos clients. Les processus de stockage et de travail structurés ainsi que l'efficacité, la transparence et la flexibilité accrues de notre entrepôt nous permettent d'envisager l'avenir avec optimisme", déclare Pekka Pöntiö, directeur de la logistique chez ETRA.
"Nous nous réjouissons de la confiance accordée par ETRA et Gebhardt et nous nous souvenons encore aujourd'hui avec plaisir de cette performance d'équipe commune, qui a bien sûr été fêtée sur place dans un sauna à la manière typiquement finlandaise", déclare Horst Reichert, directeur général de S&P Computersysteme GmbH.